Fast Facts
Two hospital locations, in Petrolia and Sarnia, ON
- 12.97% Average reduction in energy use*
- 11.71% Average reduction in natural gas use*
- 325 Beds approximately
- 130K Residents
- 80K+ Ambulatory care visits (2019-2020)
- 73K+ Visits to emergency departments (2019-2020)
- 10K+ Surgical cases (2019 - 2020)
- 1 Maintenance dashboard, 1000 data sources
Over a 4 month period*
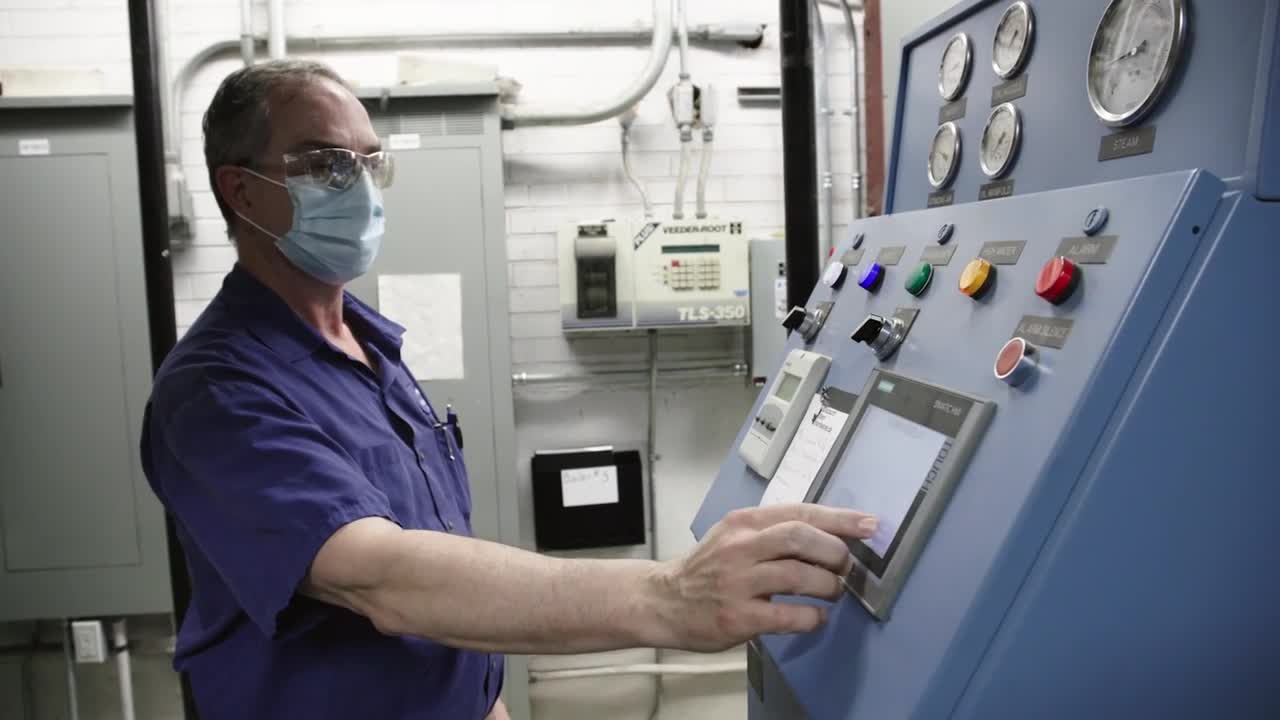
- Are the operating rooms’ heating and cooling systems performing as required to prevent downtimes?
- Is mechanical equipment properly maintained to avoid exposures to hazards?
- Are utilities being optimized to allow more of the hospital’s limited resources to be spent on patient care?
- If power is lost to the building, will emergency generators be ready to do their job?
SUSTAINABILITY IN HEALTHCARE
Such was the case with Bluewater Health, a Canadian healthcare facility with hospitals in Petrolia and Sarnia, Ontario. The organization features a 10-year-old redevelopment and addition to a 60-year-old building and a 110-year-old building in the midst of redevelopment. The 317,000 sq. ft. addition to the facility in Sarnia featured a significantly larger emergency department; a surgical center with eight operating rooms and four procedure rooms and a consolidated maternal/infant/child program, with labor, birthing and pediatric services all on one floor. The new construction also incorporated many innovative and sustainable design features, such as an underground cistern to collect rainwater, a grey water system for toilets, a state-of-the-art chiller and a new combined heat and power generating plant ready to come online. This makes Bluewater Health one of Canada’s first LEED (Leadership in Energy and Environmental Design) certified hospitals. Bluewater Health then leveraged Honeywell Forge Energy Optimization; a cloud-based AI solution that autonomously manages HVAC energy use based on numerous demand factors. The solution captures real-time building data across an entire building portfolio and calculates the optimal set-point strategy for each building, then automatically adjusts the set-points without human intervention.
NEW FACILITY, NEW CHALLENGES
But even these impressive new features can’t solve every facility challenge. As with any institution, dealing with budgets and making finances spread across every need is always a concern. And with all these new sustainable, digital features comes the challenge of consolidating many inputs of information and technology into one stream of collection and output. In addition, Bluewater Health spanned two locations, with varying infrastructure, making consolidation an even bigger issue. To solve these challenges and many others, Bluewater Health leaned on its commitment to innovation and providing safe, quality care. One of the main drivers behind this new project was the desire to be more proactive on repairs and efficiencies – before they even became an issue. The Bluewater Health team wanted to perform more than digital maintenance, or even preventative maintenance. They wanted to perform predictive maintenance. To put it in healthcare terms, predictive maintenance is very much like preventative medicine.
It’s far smarter, more efficient and more cost effective to catch a medical issue before it presents any symptoms or actual harm. Predictive maintenance is similar. By learning from operating data that was already available, they would be able to see issues before they became problems. That’s why Bluewater Health sought an intelligent platform that could work with, learn from and grow with their current systems. By having such a platform in place, facilities and maintenance staff would be able to curtail any issues before they arose, and focus on increasing efficiencies.
MANY SOURCES, ONE DASHBOARD
When implementing the Honeywell Forge solution the Bluewater Health team reviewed their systems with Honeywell technicians, laid out a direct plan on where the critical start areas were and put rules into effect that would bring about the best analysis -- quickly. Once implemented, Honeywell Forge began to analyze all of the data that is already obtained from EBI (our Building Automation System) and gave feedback on what was not operating optimally based on the created rules. The new system began to pull from over 1000 sources of information and almost instantly provided feedback on anything giving readings outside the acceptable range. One surprise was that while the systems seemed to be running extremely well overall, the problems that did arise all had one certain “trigger” in common. Once that small issue was resolved, the other larger ones would be as well. There were also financial benefits. For instance, by changing air filters in the hospital only when they truly needed to be changed, it’s possible for staff to get another six more months or a year out of existing filters. That’s a great potential for cost savings.
A COMFORTING OUTCOME
Bringing in the Honeywell team and Honeywell Forge obviously had technical and financial benefits. By being able to monitor a multitude of data streams, the organization saved money and clearly achieved efficiencies. But there was another, very human, benefit to the project as well. The maintenance staff express increased job fulfillment as they spend more time performing regular, planned maintenance and strategizing about how to improve systems, rather than reacting to concerns reported by frontline staff. Being able to monitor hydro and gas consumption on a daily basis is also extremely helpful. They are now able to monitor and track live maintenance data through a dashboard showing trends, vulnerabilities and predictive comfort levels. This in turn has increased the comfort level for staff, since they could be more confident that everything from the operating rooms to the chemotherapy prep areas, and the isolation rooms to the infant nurseries were all working optimally. The peak performance of systems coupled with the predictive corrective measures ensure that the patients themselves enjoy the cleanest, most ideal temperature-controlled rooms and enhance both their healthcare experience and overall comfort level. And finally, of course, the support services manager’s role is now more proactive. By having all that data, and all the answers to their burning questions, the manager can spend more time proactively caring for these impressive facilities that provide care for the community.